Impact, Hardness and Fracture Morphology of Aluminium Alloy (Al-Si) Filled Cobalt Oxide Nanoparticles at Various Stir Casting Temperatures
DOI:
https://doi.org/10.37934/mjcsm.5.1.1120Keywords:
Stir-Casting, Al-Si, CoO nanoparticles, impact toughness, hardness, fracture morphologyAbstract
The automotive and aviation fields require engineering materials that can save and optimise fuel consumption. Unique characteristics of lightweight, higher strength to weight ratio, good corrosion resistance, and good castability are indispensable for castable metal such as Silicon Aluminium (Al-Si). The mechanical properties of Al-Si could be further improved through the addition of Cobalt Oxide (CoO) nanoparticles during the casting process. The importance and purpose of this study were to determine the impact toughness, hardness and fracture morphology of Al-Si metal alloy filled with 0.015 wt.% CoO nanofiller at the various melting temperature of 750 °C, 800 °C and 850 °C. The stir casting method was utilised considering the most appropriate method for mixing nanoparticles powder into the Al-Si matrix. Three test specimens were prepared for each temperature variation. Impact testing using the Charpy method (ASTM E23-56 T) and hardness testing using Rockwell Superficial HR15T and fracture morphology obtained from impact testing fractures were performed accordingly. The impact test results showed that the Al-Si added with 0.015% CoO at 800 °C of melting temperature possessed the highest impact toughness value of 25.111 x 10-3 Joule mm-2 than the other variations. The hardness test results showed that Al-Si added 0.015% CoO with a melting temperature of 850 °C had the highest hardness value of 79.52 HR15T. The fracture morphology of the impact test in all specimens shows uniform brittle fracture characteristics. It is found that the melting temperature during the stir-casting process of Al-Si has played a significant role in influencing the resulted properties of Al-Si filled CoO nanoparticles metal matrix composites. The selection of an accurate melting temperature for the stir casting process will affect the resulted properties of produced metal composites.
Downloads
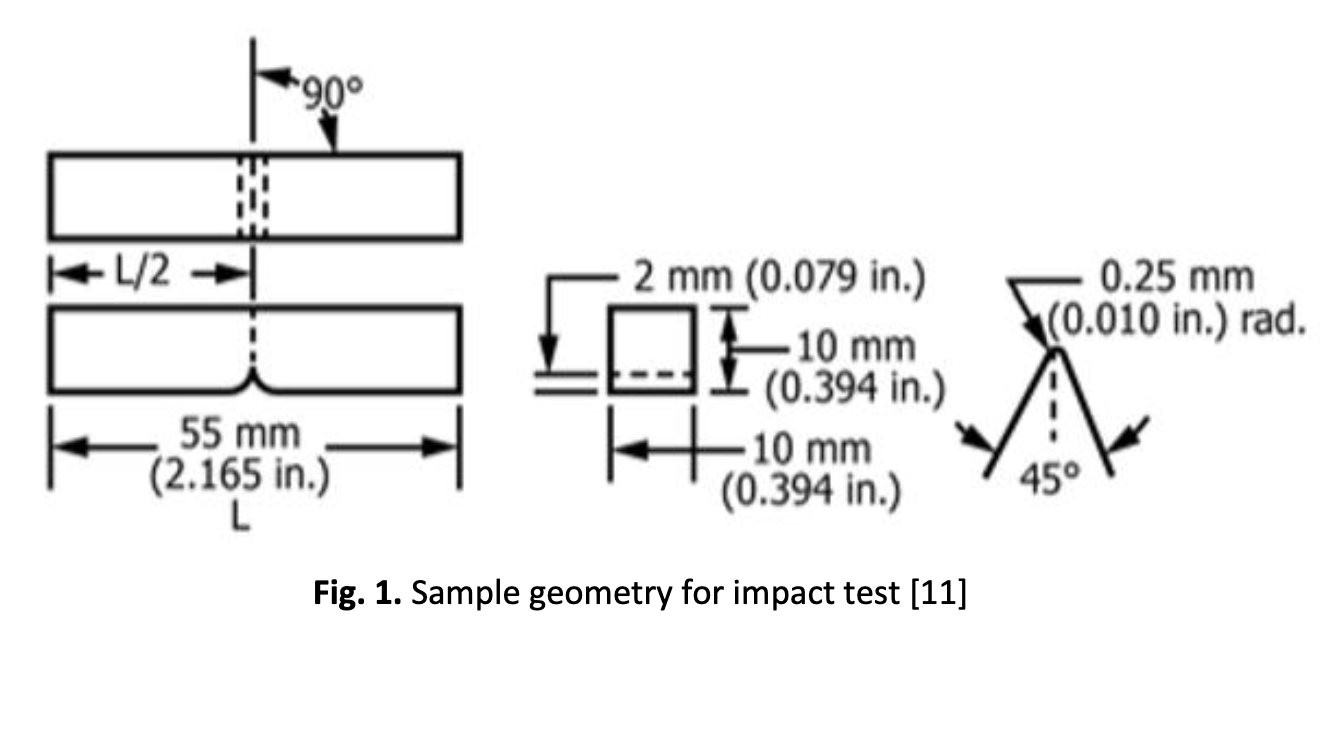