Taguchi Method-Based Optimization of Single-Pass Abrasive Waterjet Cutting of Thick Aluminium
DOI:
https://doi.org/10.37934/mjcsm.16.1.6068Keywords:
Abrasive Waterjet Machining, Taguchi Method, Process Optimization, Traverse Speed, Waterjet Pressure, Stand-Off DistanceAbstract
Cutting force attenuation in AWJ induces surface defects (high Ra, large theta) in metals and delamination in composites, especially in thick sections that limiting industrial adoption and requiring post-processing. A robust Taguchi experimental design was employed to optimize AWJ cutting parameters to minimize these issues when cutting thick aluminium blocks. An L8 orthogonal array with three factors; waterjet pressure (WP), stand-off distance (SOD), and traverse speed (TS), each at two levels, was used and analyzed via Minitab software. Other parameters remained constant: nozzle diameter (1.0 mm), abrasive size (80 mesh), and abrasive flow rate (0.3 kg/min). Traverse speed was found to be the most critical factor affecting Ra and theta, though waterjet pressure and stand-off distance also had significant impacts. The optimal parameters, higher waterjet pressure (315 MPa), lower traverse speed (38 mm/min), and lower stand-off distance (3 mm), yielded the best results for both Ra (4.2 µm) and theta (1.24°). In conclusion, the interaction of optimized AWJ parameters enhances kinetic energy and momentum transfer, improving material removal efficiency and cutting surface quality. The study systematically evaluates critical abrasive waterjet parameters to optimize cutting strategies, demonstrating applicability for thick aluminium and diverse material types.
Downloads
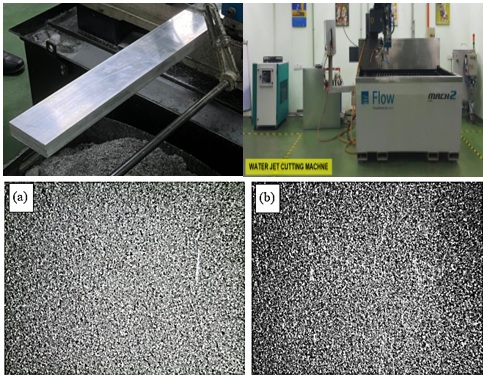