Experimental and Numerical Study of Conical-Shaped Pin Finned Heat Sink with PCM Material
DOI:
https://doi.org/10.37934/mjcsm.14.1.0115Keywords:
Heat sink, Fins, PCM, 3D computer model, Transient simulationAbstract
Many researchers have recently become interested in phase change material (PSM) for passive cooling of electronic equipment. The performance of PCM is enhanced by using fins as thermal conductivity enhancers (TCE). For a heat flux of 20,000 W/m2, three-dimensional numerical (transient) analyses were conducted for pin (Circular) and conical-shaped fins with and without holes and dimples on the surfaces to investigate the heat transfer by natural convection. Paraffin wax was used as the PCM material within the fins' spaces by keeping 9% volume of the fins and 91% volume of PCM of the total space above the base plate. The transient heat transfer performance of fins is observed for 20 minutes. Surface areas, temperature curves, liquid fraction curves, and theta versus Fourier number curves were compared to analyze the effect of fins of different shapes on the heat transfer rate. Conical-shaped fins with dimples and holes showed the best cooling performance with a 4.6% increment of heat transfer compared with conventional pin (circular shape) fins. With and without PCM, conical fins were subjected to experimental investigation for 20 minutes. Mild steel was the heat sink material, and paraffin wax was the PCM material. Heat flux of 4000 W/m2 was given to the heat sink’s base by a heater. The acrylic glass was used for insulation. The temperature was recorded for nine fins at different heights. In the experiment, the case with PCM gave 5% to 8% better cooling performance than the case with air. The study shows that using conical fins with dimples and holes (a unique fin shape) in PCM-based heat sinks can produce superior thermal performance compared to traditional (circular-shaped) pin-fins.
Downloads
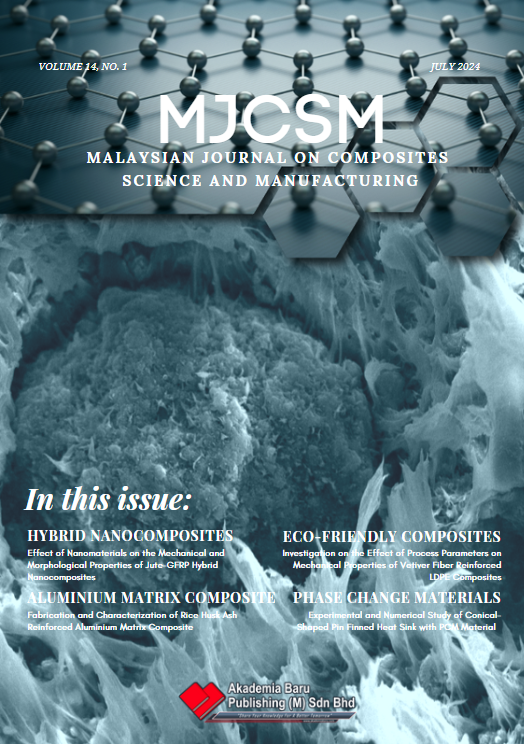