Dynamic Characterization of Composite Liner-less tank with Geodesic-Isostrain Dome Contour
DOI:
https://doi.org/10.37934/mjcsm.11.1.118Keywords:
Filament winding, Modal parameters, Finite Element Analysis, Type-V, Composite Liner-less TankAbstract
The article describes the design, realization and experimental methodology to determine the modal parameters for the composite liner-less tank, which plays an important role in the study of the structural response of the tank. The design of composite liner-less tank is determined by the strain’s transverse to the direction of the fibres, and the tank must be able to contain the pressurized fluid without leakage under all given loading conditions. In the present work, a geodesic-Isostrain dome contour for a liner less carbon epoxy composite tank is determined. The tank is realized by filament winding using an epoxy resin system on a 4-axis CNC filament winding machine. The calculated value of the modal assurance criteria (MAC) for the 1st natural mode is 0.802275, which validates the finite element modelling and analysis approach for the realized tank. To determine the damping coefficient, free vibration tests were performed at the specimen level. The damping coefficients for the tank and the 90-degree specimens agree well, indicating that the resin system determines the damping of the tank in free –free condition. The tank was successfully pressurized to 12 bars with no leakage. The impulse hammer excitation method was used to determine the natural frequencies at different pressure values and found comparable with the finite element simulation results.
Downloads
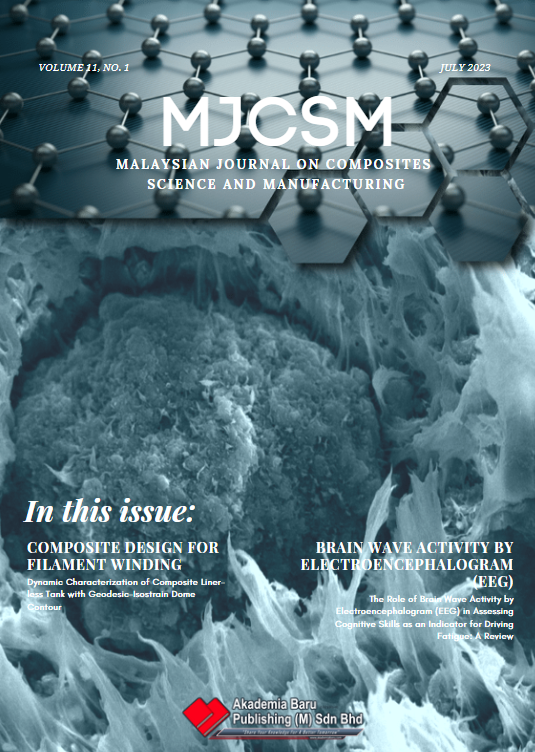