A Mesh Convergence Study for 2D Axisymmetric Pipe Wall Thickness
DOI:
https://doi.org/10.37934/armne.23.1.7790Keywords:
Numerical, equivalent stress, mesh convergence study, 2D axisymmetricAbstract
A meshing size study is essential for any simulation, as it affects the accuracy of the results by approximating the real-world geometry. This paper presents a detailed mesh convergence study for a 2D axisymmetric pipe model. The model incorporates a one-quarter cross-section due to the axisymmetric nature of the pipe. Four pipe wall thicknesses were investigated: 3.40 mm, 7.11 mm, 10.97 mm, and 18.26 mm. The results revealed a significant advantage for simulations involving thin pipes. They achieved convergence, a state with stable solution values, by utilizing a less dense mesh, leading to reduced computational time. This trend was exemplified by the fact that a thinner pipe with thickness, t = 3.40 mm has converged with only 8 mesh elements, whereas a significantly thicker pipe, t = 18.26 mm necessitated 14 elements for convergence. This suggests that more complex geometries, with intricate details, may require a larger and denser mesh for convergence, leading to increased computational time. In conclusion, the mesh convergence study confirms that the finite element analysis (FEA) model has achieved a converged solution.
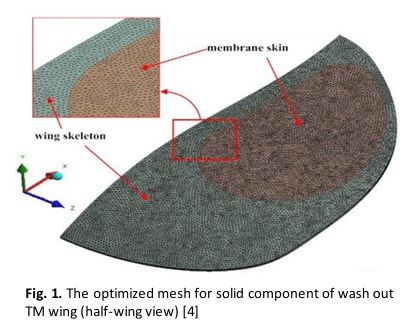