Superhydrophobic Surface of Ti6Al4V using Direct Nanosecond Laser Texturing
DOI:
https://doi.org/10.37934/armne.17.1.117132Keywords:
Ti6Al4V, laser texturing, wetting behaviour, superhydrophobicAbstract
This study aims to investigate the impact of laser parameters, including laser power, laser frequency, laser scan speed, and hatches line distance, on Ti6Al4V to create superhydrophobic surfaces. Surface profile and roughness play vital roles in achieving superhydrophobicity, and existing laser surface modification methods are time-consuming and lack subsequent steps for optimizing desired characteristics. A factorial design was implemented, varying laser power (12 and 18 W), laser frequency (40 and 60 kHz), laser scan speed (180 and 220 mm/s), and hatch line distance (0.25 and 0.45 mm). Surface morphology and topological properties were analyzed for surface characterization. The results demonstrate a significant increase in surface roughness profiles such as Sa and Sq by 6 and 5 times, respectively, compared to the untextured surface. These modifications also led to enhancements in surface topological properties. Regression analysis revealed the importance of controlling the surface profile for achieving superhydrophobicity. Statistical analysis indicated that laser power, laser frequency, and laser speed were the most significant parameters contributing to superhydrophobicity. The optimum laser parameters for superhydrophobic surfaces were determined as 18 W laser power, 40 kHz laser frequency, and 220 mm/s laser scan speed. In conclusion, this study emphasizes the critical role of surface topological properties in creating superhydrophobic surfaces on Ti6Al4V. Laser texturing techniques successfully improved surface roughness and profile, facilitating the development of superhydrophobic surfaces. These findings offer valuable insights for advancing surface engineering, with potential applications in the aerospace, automotive, and biomedical industries.
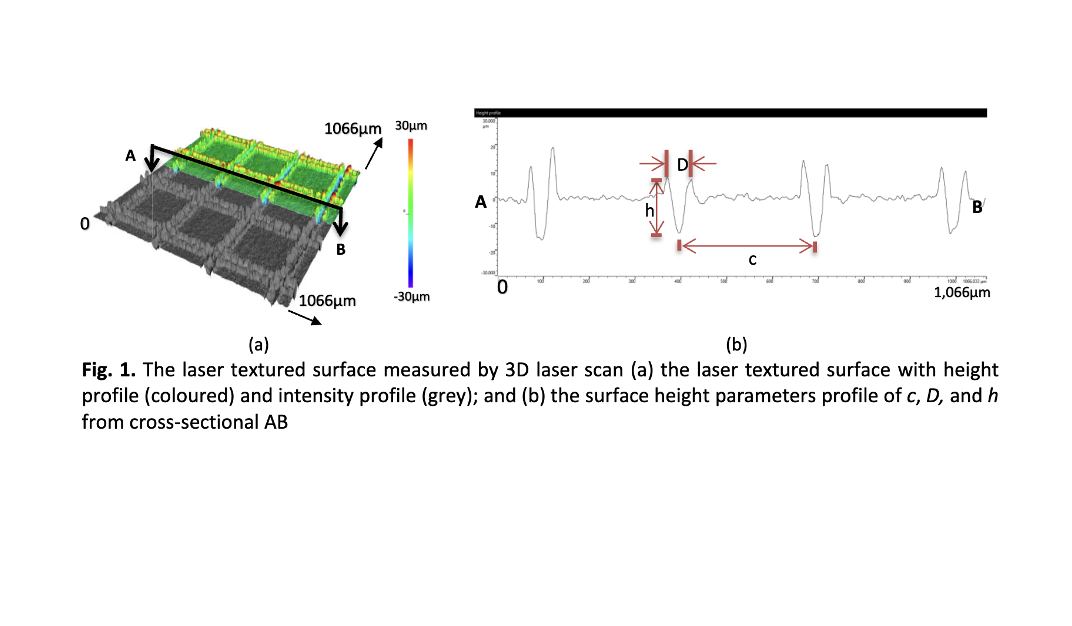